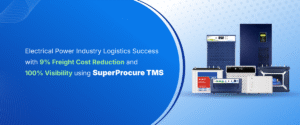
Electrical Power Industry Logistics Success with 9% Freight Cost Reduction and 100% Visibility Using SuperProcure TMS
Case Study Electrical Power Industry Logistics Success with 9% Freight Cost Reduction and 100% Visibility
Case Study Electrical Power Industry Logistics Success with 9% Freight Cost Reduction and 100% Visibility
Table of Content : Executive Summary: Why FMCG Supply Chains Struggle with OTIF If you’re leading logistics in
Key Takeaways: How TMS Integration Transforms Logistics Operations
A Transportation Management System (TMS) is powerful but only when it’s connected.
Modern supply chains often rely on disjointed systems for planning, dispatch, inventory, and billing. That leads to:
Platforms like SuperProcure solve this through a plug-and-play ILMS layer that unifies all logistics touchpoints from order planning to invoice reconciliation into one synchronized digital flow.
Problem Area | What Happens Without Integration | Business Impact |
S&OP to Dispatch | Manual data flow, slow vehicle planning | Delays, missed orders |
ERP Orders in TMS | Duplicate/manual data entry | Time wasted, errors, inefficiency |
Vehicle & Driver Info | Unverified uploads, no real-time checks | Compliance risk, fraud |
Gate Logs | Excel or paper-based entries | No visibility, congestion |
Dock Scheduling | No coordination with dispatch | Truck pileups, loader inefficiencies |
Shipment Tracking | Dependent on calls or WhatsApp | Missed SLAs, escalations |
Invoicing | Disputes due to mismatched data | Payment delays |
Compliance (e-Waybill, etc.) | Manual extensions or last-minute actions | Penalties, stress |
Weighbridge Entries | Repetition across systems | Redundancy, audit risk |
Book a quick walkthrough of SuperProcure: Book a Demo
An ILMS acts as the central nervous system of logistics integrating multiple systems to enable real-time orchestration.
SuperProcure’s ILMS framework, for example, offers native integrations with:
This allows enterprises to eliminate operational silos and manage logistics across functions without switching tools.
Let’s break down the 7 essential systems your TMS must integrate with and how solutions like SuperProcure help enable this:
Why it matters: Your ERP is the source of truth for orders, inventory, and finances. But without real-time sync, order fulfillment can become slow and error-prone.
Integration unlocks:
Business impact: Your finance, sales, and logistics teams stay aligned without needing daily coordination calls or emails.
Why it matters: Demand planning only works if it’s grounded in supply-side realities. Without live logistics data, forecasts can easily break down.
Integration unlocks:
Business impact: Avoids last-minute scrambles, overbookings, or underutilised fleets.
Why it matters: Customers expect updates in real time. But if your customer support team doesn’t have logistics visibility, it hurts service quality.
Integration unlocks:
Business impact: Fewer escalations, faster responses, and improved CX.
Why it matters: Warehouse operations and transportation are closely intertwined. Yet, many teams still manage them in silos.
Integration unlocks:
Business impact: Reduced loading delays, faster turnarounds, and better dock utilization.
Why it matters: Live tracking is basic now. True visibility means more than just knowing the truck’s location.
Integration unlocks:
Business impact: Better control, proactive issue handling, and reliable delivery commitments.
Portal | Why It Matters | What Integration Unlocks | Business Impact |
VAHAN (India’s national registry for vehicle data) | Manual vehicle document verification is slow, error-prone, and often skipped, risking legal issues and delays. | – Automated vehicle verification and onboarding- Regulatory compliance checks (insurance, permits)- Reduced manual data entry and fraud risk | – Faster vehicle assignment- Improved compliance- Lower risk of on-road detention or fines |
SARATHI (Driver license records portal) | Manual or informal driver verification causes compliance gaps and safety risks. | – Real-time driver credential verification- Up-to-date compliance logs for audits- Faster driver onboarding via API | – Quicker transporter onboarding- Lower safety risks- Stronger regulatory compliance |
e-Waybill Extension Portal (GST-integrated platform) | Expiring e-Waybills during transit create legal liabilities; manual extensions are slow and stressful. | – Automated e-Waybill extensions- Continuous legal documentation for goods in transit- Route-planning integration to trigger extensions | – Avoids non-compliance fines- Ensures uninterrupted goods movement- Reduces operations team workload |
IoT Integration Type | Why It Matters | What Integration Unlocks | Business Impact |
Weighbridge Integration | Manual weighbridge data entry causes delays, human errors, and compliance issues. | – Eliminates manual errors & fraudulent weight reporting- Automates gate check-in/check-out- Instantly triggers trip sheets & gate passes | – Immediate over/underloading alerts- Compliance with regulations- Prevents penalties |
RFID Integration at Plant Entry/Exit | Manual gate entries cause congestion, missed records, and slow yard movement. | – Contactless & fast vehicle check-in/out- Auto-captures vehicle movement for audit trails- Improves yard management | – Reduced congestion- Faster turnaround time (TAT)- Full traceability across shifts |
Temperature & Humidity Sensors (Cold Chain) | Temperature-sensitive goods risk spoilage & SLA breaches without real-time monitoring. | – Real-time alerts for temperature deviations- Compliance with pharma & food regulations | – Prevents spoilage- Ensures SLA adherence- Enables proactive maintenance actions |
Any TMS can claim to integrate. But what matters is:
Platforms like SuperProcure answer “yes” to all three, making it ideal for connected logistics transformation.
Book a quick walkthrough of SuperProcure: Book A Demo
Subscribe to our blog for the latest news and updates
Ensure your company’s data is completely secure and compliant with the latest regulatory standards
5/5
4.5/5
5/5
4.5/5
Solutions
Industry
Real Time Freight Sourcing And Collaboration Platform
Unit 3B, 4 Bakul Bagan Row, Lansdowne Market. Kolkata- 700025, India
Share us the details to connect to a relevant team member.